Aluminum extrusions can be finished in various ways to enhance their appearance, durability, and performance. Here are eight different surface finishes commonly used on aluminum extrusions:
Mill Finish: This is the natural finish that aluminum extrusions have after they are manufactured. It’s essentially the raw, untreated surface of the aluminum. It has a matte appearance and may exhibit slight variations in color and texture.
Anodizing: Anodizing is a popular surface treatment for aluminum extrusions. It involves creating a controlled oxide layer on the surface of the aluminum through an electrolytic process. Anodizing provides increased corrosion resistance, improved wear resistance, and the ability to apply various colors.
Powder Coating: Powder coating is a method where a dry powder is electrostatically applied to the aluminum surface, and then the extrusion is heated to fuse the powder into a smooth, durable, and colorful coating. It offers excellent weather resistance and a wide range of color options.
Painting: Aluminum extrusions can also be painted using liquid paint. This provides a high level of customization in terms of color and finish. However, the paint may not be as durable as some other finishes, especially in outdoor environments.
Polishing: Polishing aluminum extrusions can create a reflective, mirror-like surface. Different levels of polishing can be achieved, from a satin finish to a high-gloss mirror finish. Polished surfaces are more decorative and less corrosion-resistant than some other finishes.
Brushing: Brushing involves using abrasive materials to create a textured or brushed appearance on the aluminum surface. It can help hide minor imperfections and scratches, making it a suitable choice for applications where aesthetics are important.
Sandblasting: Sandblasting involves propelling abrasive particles at high speed onto the aluminum surface to create a textured finish. This finish is often used to create a matte, non-reflective surface that can help mask imperfections.
Chemical Etching: Chemical etching involves applying a chemical solution to the aluminum surface to create a controlled level of corrosion. This can be used to achieve specific textures, patterns, or designs on the surface of the extrusion.
Keep in mind that the suitability of a particular surface finish depends on the intended use of the aluminum extrusion. Factors like aesthetics, durability, corrosion resistance, and the environment in which the extrusion will be used should all be considered when selecting a surface finish.
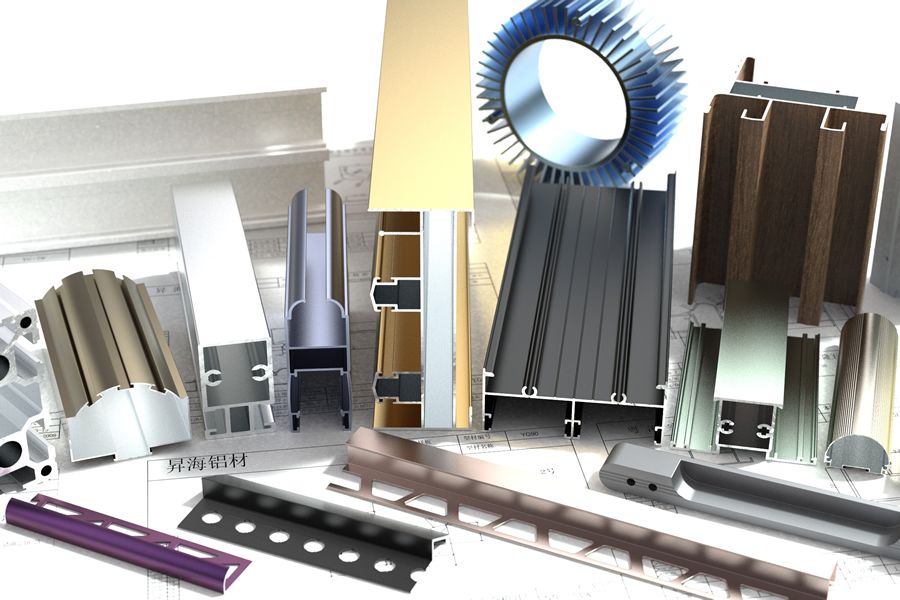
How to choose the right surface treatment for your aluminum profile?
Choosing the right finish for your aluminum extrusion involves considering several factors, including the desired aesthetics, functional requirements, environmental conditions, and budget. Here are some steps to help you make an informed decision:
Define Your Goals:
Determine the primary goals for the finish. Are you looking for improved corrosion resistance, aesthetic appeal, better wear resistance, or a combination of these factors?
Environmental Conditions:
Consider the environment in which the aluminum extrusion will be used. If it will be exposed to harsh weather conditions, high humidity, or corrosive substances, prioritizing corrosion resistance becomes important.
Aesthetic Requirements:
Different finishes offer varying levels of visual appeal. Consider whether the extrusion will be visible and whether you want a natural metallic look, a specific color, or a particular texture.
Functionality:
Determine any functional requirements for the finish. For instance, if the extrusion will be subjected to high wear or abrasion, a more durable finish might be necessary.
Types of Finishes:
There are several common finishes for aluminum extrusions:
Anodizing: This is a popular finish that provides corrosion resistance, improved wear resistance, and can be dyed to achieve various colors. Anodized finishes come in different levels of thickness, providing varying degrees of protection.
Powder Coating: Powder coating offers a wide range of colors and finishes, including matte, glossy, and textured. It provides good corrosion resistance and durability.
Painting: Aluminum extrusions can be painted for aesthetic purposes. However, painting might not offer the same level of protection as other finishes.
Electrostatic Dissipative (ESD) Coatings: If your application requires protection against electrostatic discharge, an ESD coating can be applied.
Chemical Film (Chromate Conversion): Also known as chromating, this process provides corrosion resistance and helps with adhesion if the extrusion will be painted later.
Mechanical Finishes: These include techniques like brushing, polishing, or sandblasting, which can create unique textures and visual effects.
Budget Considerations:
Different finishes come with varying costs. Consider your budget and balance it with the desired level of protection and aesthetics.
Testing and Samples:
It’s often a good idea to test different finishes on a small scale or request samples from finishing suppliers. This allows you to evaluate the appearance, durability, and performance of each finish option.
Consult Experts:
If you’re unsure about which finish to choose, consult with experts in aluminum extrusion finishing or suppliers who can provide guidance based on your specific needs.
Regulations and Standards:
Depending on your industry and application, there might be regulations or industry standards that dictate the type of finish you should use. Make sure to consider any relevant requirements.