The choice of the best aluminum fabrication process for your project depends on several factors, including the specific requirements of your project, the type of aluminum alloy being used, the desired end product, budget constraints, and production volume. Here are some common aluminum fabrication processes along with their strengths and suitable applications:
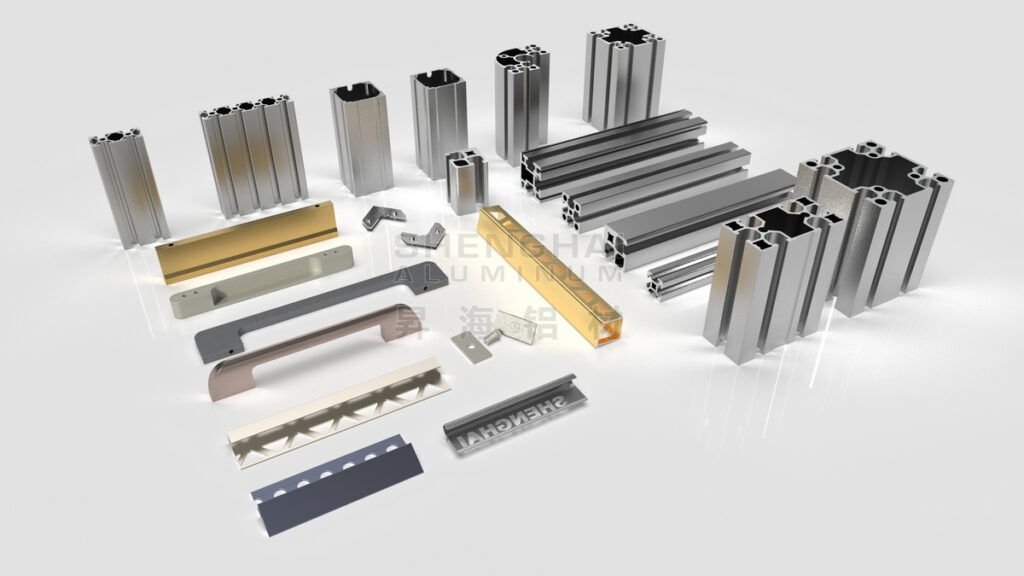
Extrusion:
Process: Aluminum extrusion involves pushing heated aluminum billets through a die to create complex cross-sectional shapes.
Strengths: Excellent for creating uniform, continuous profiles with high precision and consistent dimensions. It is cost-effective for producing long, constant cross-section parts.
Suitable Applications: Frames, rails, tubing, heat sinks, and other linear or curved shapes.
Sheet Metal Forming:
Process: Sheet metal forming involves cutting, bending, and shaping flat aluminum sheets to achieve the desired form.
Strengths: Versatile, widely available, and suitable for both low and high-volume production. It can create a variety of shapes and sizes.
Suitable Applications: Enclosures, panels, automotive parts, brackets, and various customized components.
CNC Machining:
Process: CNC (Computer Numerical Control) machining involves using computer-controlled machines to remove material from aluminum blocks to create precise parts.
Strengths: High precision, excellent surface finish, and suitable for small to medium production runs. It can handle complex geometries.
Suitable Applications: Prototypes, small-batch production of intricate parts, aerospace components, and functional prototypes.
Welding:
Process: Aluminum welding uses various techniques like MIG (Metal Inert Gas), TIG (Tungsten Inert Gas), or laser welding to join aluminum components.
Strengths: Ideal for joining aluminum parts permanently. It offers strong and durable connections.
Suitable Applications: Aerospace, automotive, marine, and other industries where strong and lightweight structures are needed.
Casting:
Process: Aluminum casting involves pouring molten aluminum into molds to create complex shapes.
Strengths: Well-suited for producing intricate designs and large components.
Suitable Applications: Engine components, decorative elements, and complex shapes for various industries.
Powder Coating:
Process: Powder coating involves applying a dry powder to the aluminum surface and then curing it to create a protective and decorative finish.
Strengths: Provides a durable, uniform finish that resists corrosion and wear.
Suitable Applications: Outdoor equipment, architectural elements, and products requiring a decorative, protective coating.
Anodizing:
Process: Anodizing is an electrochemical process that enhances the aluminum’s surface by forming an oxide layer, providing improved corrosion resistance and other benefits.
Strengths: Improves surface hardness, wear resistance, and corrosion resistance.
Suitable Applications: Aerospace, electronics, architectural elements, and outdoor applications.
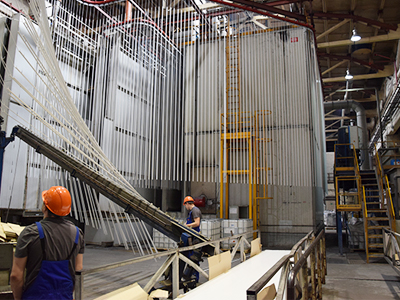
When choosing the best aluminum fabrication process, consider factors such as design complexity, required tolerances, material properties, lead time, and budget. Consulting with experienced Shenghai Aluminum fabricators or engineers can also help you make an informed decision based on your specific project requirements.